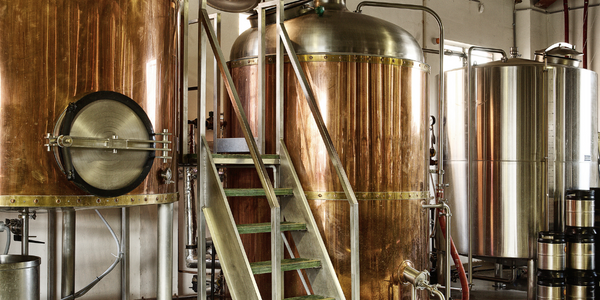
- Application Infrastructure & Middleware - Database Management & Storage
- Food & Beverage
- Business Operation
Data management system versiondog, an indispensable instrument in operations engineering at Warsteiner. Preventive maintenance has long been the norm at the Warsteiner Brewery. And yet, unplanned maintenance activity can still occur. It is therefore of great importance that the latest update version for each and every PLC be stored centrally. In this industry, there is no time to waste trying to conduct a search.
Dipl.-Ing.Thomas Wenthaus works at the Sauerland based family enterprise, the Warsteiner Group, in the operative engineering department. The "Automators", a term which Wenthaus lovingly uses to describe his department, help to manage the existing process systems for the system control, optimise processes and develop new processes in cooperation with the company's other departments, especially in the cases of additional production facilities or new production lines. lant maintenance and restarting machines and plant components are also part of the good management of plant processes. It used to be that different departments of the company each had their own system of maintenance, repair and operations, and that access to each of these was organised differently. Since then the company has switched to the version control solution product versiondog. Wenthaus had already worked with an earlier version control system, "VersionWorks". "Even then", he says, "we were searching for a way in which to ensure that PLC projects were safeguarded and versioned." At the beginning, each individual department used to save the current data for each PLC. Gradually, a versioning and data management system was introduced across more and more departments until it had been incorporated by all of them: "Today, it's impossible to imagine working without it. Having a centralised data storage system means that there is a complete change history to which all 60 users have access from whichever department they may be in," says Wenthaus. Indeed, in addition to the brewery in Warstein yet another brewery belonging to the enterprise group has integrated versiondog. From now on, the management of PLC programs from all other locations will take place centrally in Warstein. All that versiondog requires is a little bit of discipline. Everyone is required to meticulously document their work. They happily do this because they recognise the benefits. Is such software cost-effective? In response to this question, Wenthaus shares an account from his own work day: "All of our machines are connected to each other via the network. If one of the machines were to come to a halt, it would affect the entire filling and bottling process." In this context, being cost-efficient means avoiding wasting time. "Thanks to versiondog, we are able to rapidly localise errors and get the plant back up and running again." He goes on to tell us that it is difficult to precisely estimate exactly how much time is saved. This is because so much depends upon where exactly the errors occur. But, he adds: "With versiondog we have the tool we need." And the same goes for Warsteiner's robots. "One wrong piece of data and the configuration work of what may amount to weeks flies out the window", Wenthaus says. "When this happens, a robot is liable to make a wrong move." As such, the calibration data required for packaging machines necessitates precise work that leaves little room for error. "The wonderful thing about versiondog is that fact that you know when exactly a particular change was made, who made it, and why it was made." All processes involved in production are controlled via a central control system. This presents a particular challenge in the filling and bottling process because not only is there a comparatively large number of individual machines, but these machines are also connected to each other. All data is centrally available for comparison. For the members of maintenance staff, this has a definite practical use. Comparison allows for errors to be detected and for the causes of malfunctions to be resolved accordingly. Managing process data in this way via a process control system is now the norm. No missed backups In the brewery's processes there is no way now that backups can be missed and data can be lost. Using the benefit of his experience, Thomas Wenthaus stresses that effectively safeguarding data and regularly creating versions are indispensable for fast and efficient disaster recovery. The data from all controllers is stored by versiondog so that it cannot be lost. In the event that an error occurs on the assembly line or if the assembly line itself suddenly stops, time becomes of the essence. Rather than wasting it looking for the problem, the malfunctioning component will be immediately swapped out. Then the appropriate software will be taken from the server with confidence, applied - and the station or plant can be restarted immediately. Being able to do this necessitates a certain amount of discipline when changing or customising a PLC: "Several colleagues of mine have had to adapt to this. But as soon as they saw how brilliant it was to be able to centrally access single project data, they accepted 'versiondog'." The server-client structure allows for any computer or programming device to be connected in order to access the data or software versions on the central server. Working with versiondog is very simple. One big benefit is that projects cannot be easily deleted. If the user has problems at first while building experience, "there is always the support hotline at AUVESY, who are there to provide immediate help." That being said: "We seldom come across any real problems. The system is very stable." tl_files/bilder/Presse/Fachartikel/warsteiner/warsteiner_shooting_tag2-614.pngversiondog also provides additional help by storing versions of device data used in the construction of a facility, including Excel documents, data lists and networking plans. This means that even when problems occur in the middle of the night, it is possible to download specific detailed plans, view connection details such as bus components and quickly fix production malfunctions without delay or additional help. The need for backups depends on the relevance of the device. Not all PLCs are backed up on a daily basis. The number of backups per average day is around 40. However, per week the number can be anywhere between 300 and 400. The "UserClient" is used to manage versions and create new projects. "We do a lot of work with the UserClient every day", Wenthaus says. In addition to using the UserClient, he also keeps a close eye on the "ReportClient", which helps when searching in detail for errors. And, as the administrator of process systems, he regularly works with the "AdminClient" in order to configure automatic backups and carry out user administration tasks. versiondog allows for a wide variety of permutations of access rights, depending on the work area and the decision-making hierarchy. Thanks to versiondog and the "Supplier Check-Out", collaboration with external companies, e.g when constructing new production facilities, runs smoother than ever. And each authorised user is able to use this function. Working with versiondog over the years has produced one notable and useful side-effect, even if, in hindsight, it might sound somewhat obvious. For new projects or production lines, operative engineers now always make sure that all the controllers are networked. "It's a great thing for our processes that all members of staff constantly have access to the latest data." adds Wenthaus. "Connecting all devices to the network means that we can easily check from the office which control programs are running on which devices and work on them as necessary. That saves resources and a lot of time."
Case Study missing?
Start adding your own!
Register with your work email and create a new case study profile for your business.
Related Case Studies.
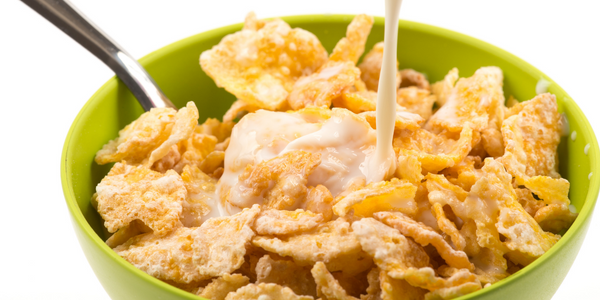
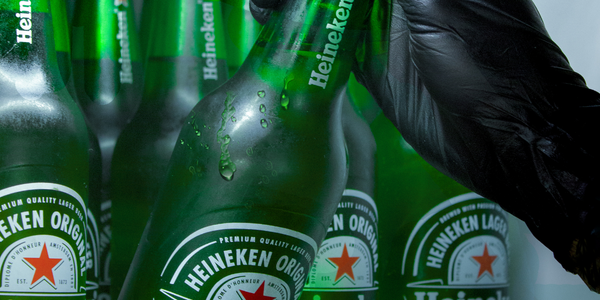
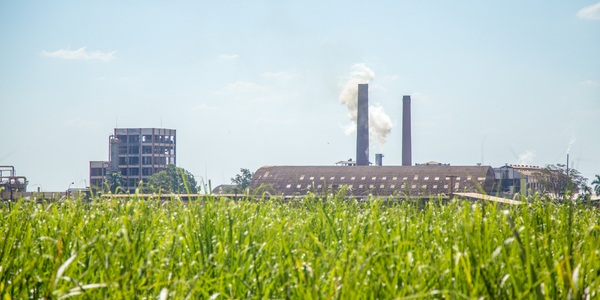
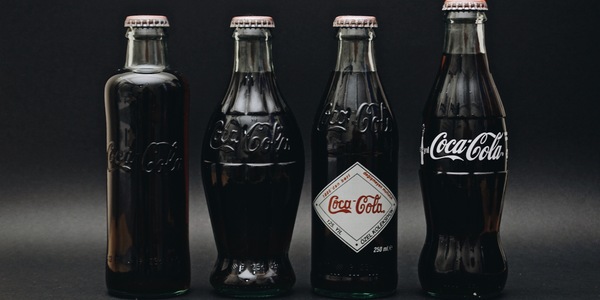
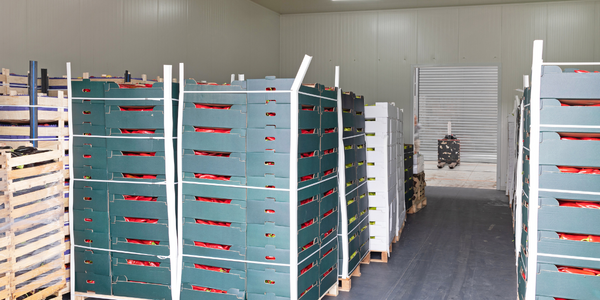
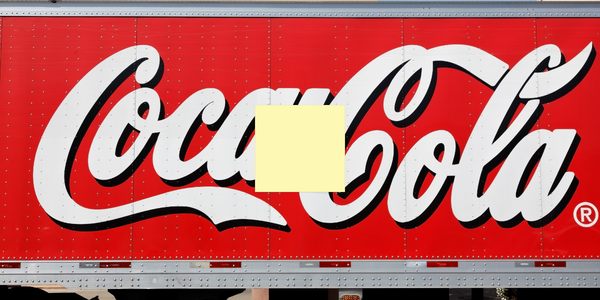