Locus Technologies
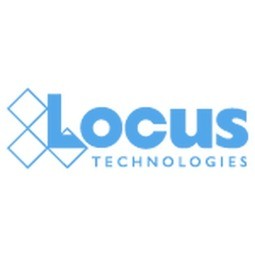
Overview
HQ Location
Canada
|
Year Founded
1997
|
Company Type
Private
|
Revenue
$10-100m
|
Employees
51 - 200
|
Website
|
Company Description
Founded in 1997 in Silicon Valley, Locus Technologies is a leading provider of enterprise Software-as-a-Service solutions, with a focus on environmental information, health, safety, and sustainability (EHS+S) compliance. We develop comprehensive software for businesses, organizations, and governmental agencies of all sizes and industries worldwide.
Locus is known for its environmental information management (EIM) system— our industry-leading software for the entire environmental sampling and analysis workflow. Our Locus Platform software provides fully configurable, next-generation applications and services, helping our clients to better manage their EHS+S operations.
At Locus, we believe the key to an organization's environmental stewardship strategy lies in its approach to data management— we design our software with this vision in mind.
Locus is known for its environmental information management (EIM) system— our industry-leading software for the entire environmental sampling and analysis workflow. Our Locus Platform software provides fully configurable, next-generation applications and services, helping our clients to better manage their EHS+S operations.
At Locus, we believe the key to an organization's environmental stewardship strategy lies in its approach to data management— we design our software with this vision in mind.
IoT Snapshot
Locus Technologies is a provider of Industrial IoT platform as a service (paas), and application infrastructure and middleware technologies, and also active in the agriculture, chemicals, cities and municipalities, food and beverage, mining, oil and gas, pharmaceuticals, recycling and waste management, renewable energy, transportation, and utilities industries.
Technologies
Use Cases
Functional Areas
Industries
Services
Technology Stack
Locus Technologies’s Technology Stack maps Locus Technologies’s participation in the platform as a service (paas), and application infrastructure and middleware IoT Technology stack.
-
Devices Layer
-
Edge Layer
-
Cloud Layer
-
Application Layer
-
Supporting Technologies
Technological Capability:
None
Minor
Moderate
Strong
Supplier missing?
Start adding your own!
Register with your work email and create a new supplier profile for your business.
Case Studies.

Case Study
GPC streamlines Clean Air Act Title V record keeping using Locus Platform
Grain Processing Corporation (GPC), a leading U.S. manufacturer of corn-based products, needed a smarter, more efficient tool to capture, track, notify, and report daily Clean Air Act Title V compliance parameters for numerous emission sources and points at their various production facilities. GPC was using SharePoint to enter over 20 daily logs at two facilities and had to address several questions per log and per shift, throughout a two-shift day. Their system had no reporting or notifications, and there was no consistency between the forms in the system. The EHS manager would spend weeks searching through information to obtain the data needed for GPC’s annual Title V certification report and other reporting needs.
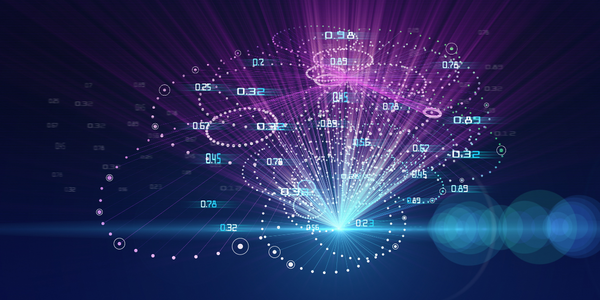
Case Study
Honeywell Enhances Data Quality and Efficiency with Locus Technologies
Honeywell, a Fortune 500 company specializing in diversified technology and manufacturing, was in need of an enterprise remediation data management system. The company sought a system that could safeguard and maintain the quality and integrity of their significant investment in generating site remediation data. They also wanted to ensure that this data was available for future use and could assure business partners of its reliable quality. Honeywell's existing data was scattered across stand-alone consultant systems, spreadsheets, and paper records, making it difficult to access and share within the company.
Case Study
Chevron centralizes data and streamlines data input and reporting with Locus’ EIM
Chevron, a leading integrated energy company, had various remediation sites spread out across multiple suppliers throughout the United States. They had no way of determining where their environmental data was or what condition it was in. They did not truly own the data that they paid for during remediation projects. Charges were incurred each time sites were transferred between consultants, and the quality and consistency of the data was not being managed properly. They needed a single repository to manage their data, unify reporting and streamline the process of generating data tables.
Case Study
San Jose Water Company automates and optimizes drinking water quality management and compliance data with Locus EIM Water software
San Jose Water Company (SJWC), a large water utility serving over a million people in the greater San Jose area, was in need of a more robust and comprehensive software solution for managing drinking water and general environmental compliance data. They were collecting routine and ad hoc samples from various activities and assets, and needed a solution to automate the entire process from sample planning to the preparation of regulatory reports. They also wanted robust data analysis tools to optimize their system operations and organizational performance, and integrated GIS to quickly view field and analytical data in real time.
Case Study
Reporting Effectively through SelfMade Mobile Applications
San Jose Water Company (SJWC) is a tech-forward company that manages dozens of internal and third-party applications. However, they faced challenges in managing their compliance programs and environmental recordkeeping. The regulations required recording company activities, which were not very predictable and involved diverse records to maintain. Before this effort, records were all managed on paper and in Excel, with no validation or backup. This made it difficult to ensure data accuracy and completeness. For example, the annual report for NPDES Discharge Reporting required hand-reviewing a full year's records, verifying data accuracy, entering it all into Excel, running analysis as required by permit, and formatting data for submission to the state.
Case Study
Honeywell achieves improves data quality, environmental risk reduction, and overall process cost reduction of over 50% with Locus’ EIM
Honeywell, a Fortune 500 diversified technology and manufacturing leader, was in need of an enterprise remediation data management system. The company required a system that could protect and preserve the integrity and quality of their substantial investment in generating site remediation data, have it available for future use, and assure business partners that legacy data is of reliable quality. Their existing data resided in stand-alone consultant systems, spreadsheets and paper records that was not readily available and shared within the company.
Case Study
GPC streamlines Clean Air Act Title V record keeping using Locus Platform
Grain Processing Corporation (GPC), a leading U.S. manufacturer of corn-based products, was struggling with an inefficient system for tracking and reporting compliance parameters for the Clean Air Act Title V. They were using SharePoint to enter over 20 daily logs at two facilities, with several questions per log and per shift, throughout a two-shift day. Their system lacked reporting or notifications, and there was no consistency between the forms in the system. The EHS manager would spend weeks searching through information to obtain the data needed for GPC’s annual Title V certification report and other reporting needs.
Case Study
Environmental Data Flow Six Sigma Process Improvement Savings Overview
The Environmental Data Flow Six Sigma improvement project was initiated in September 2009, driven by a cost-benefit analysis on data validation conducted earlier that year. The project aimed to improve LANL’s environmental data processing following receipt from the analytical laboratories. The project identified thirty-three process improvements, broken into seven subgroups. However, six of the improvements were never implemented, and two of the seven improvement subgroups did not lead to any cost savings but did lead to more accurate sample planning and increased transparency into the system.
Case Study
Del Monte effectively meets sustainability goals through improved data validation and customized reporting with Locus’ ePortal
Del Monte Foods, a large manufacturer and marketer of processed foods in the U.S., was struggling to meet its sustainability goals due to issues with data validation and manual report creation. The company was exporting data to spreadsheets to create reports, a process that was time-consuming and prone to errors. Del Monte needed a solution that would simplify reporting, ensure data quality, and make data more transparent within the company.
Similar Suppliers.
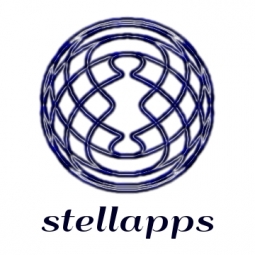
Supplier
Stellapps Technologies
Stellapps is an end-to-end dairy technology solutions company – the first of its kind in India. They are an IIT-Madras incubated company founded by a group of IITians and technologists with a strong industry background and rich experience including IIT-Madras, IIT-Kharagpur and IIM-Ahmedabad alumni, with over 18 years of Industry experience across Wipro, Nortel, Ericsson, Alcatel-Lucent, AT&T, Vodafone, Telstra, Bharti-Airtel, Aircel, Avaya, Cisco et al. Stellapps produce and procure comprehensive farm optimization and monitoring support, which helps dairy farmers and cooperatives maximize profits while minimizing effort. Stellapps is funded by Omnivore Capital – a fund anchored by Godrej Agrovet Limited and investment patrons include a large group of IIT alumni.
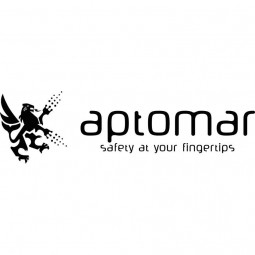
Supplier
Aptomar
Aptomar is a leading provider of Integrated Field Monitoring sensors, systems and services for the oil and gas industry. The company focuses on protecting the safety and integrity of people, the environment and assets by managing; 24/7 oil spill detection and combating, surveillance and security as well as search and rescue in close cooperation with Industry. Year founded: 2005

Supplier
Chatsworth Products
Chatsworth Products (CPI), an Anixter Technology Alliance Partner, is a global manufacturer providing voice, data and security products and service solutions that optimize, store and secure technology equipment. CPI Products offer innovation, configurability, quality and value with a breadth of integrated system components, covering virtually all physical layer needs.
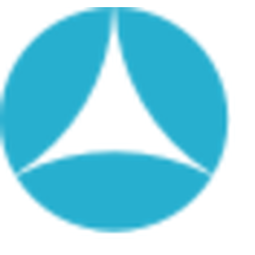
Supplier
Connexxs
Connexxs is the forth in a line of companies founded, managed or coordinated by Connexxs executives. Our first company grew from a need we saw in the operations of large natural gas fired cogeneration plants we developed. In those plants we needed an automated means to know how much gas we had available to use during each day and on what pipeline it would be delivered, if called upon.From the cogeneration experience we co-founded a company that now remotely monitors over 6,000 natural gas compressors throughout the US and Canada. This company uses both the cell data networks and satellite communications to provide its customers with the best service at the lowest costs.