Locus Technologies
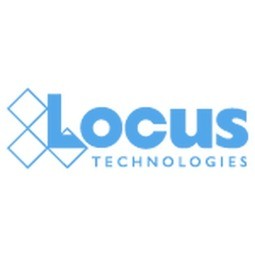
概述
总部
加拿大
|
成立年份
1997
|
公司类型
私营公司
|
收入
$10-100m
|
员工人数
51 - 200
|
网站
|
公司介绍
Locus Technologies 于 1997 年在硅谷成立,是领先的企业软件即服务解决方案提供商,专注于环境信息、健康、安全和可持续性 (EHS+S) 合规性。我们为全球各种规模和行业的企业、组织和政府机构开发综合软件。 Locus 以其环境信息管理 (EIM) 系统而闻名,该系统是我们用于整个环境采样和分析工作流程的行业领先软件。我们的 Locus Platform 软件提供完全可配置的下一代应用程序和服务,帮助我们的客户更好地管理他们的 EHS+S 运营。在 Locus,我们相信组织环境管理战略的关键在于其数据管理方法——我们在设计软件时考虑到这一愿景。
物联网应用简介
技术栈
Locus Technologies的技术栈描绘了Locus Technologies在平台即服务 (paas), 和 应用基础设施与中间件等物联网技术方面的实践。
-
设备层
-
边缘层
-
云层
-
应用层
-
配套技术
技术能力:
无
弱
中等
强
Supplier missing?
Start adding your own!
Register with your work email and create a new supplier profile for your business.
实例探究.

Case Study
GPC streamlines Clean Air Act Title V record keeping using Locus Platform
Grain Processing Corporation (GPC), a leading U.S. manufacturer of corn-based products, needed a smarter, more efficient tool to capture, track, notify, and report daily Clean Air Act Title V compliance parameters for numerous emission sources and points at their various production facilities. GPC was using SharePoint to enter over 20 daily logs at two facilities and had to address several questions per log and per shift, throughout a two-shift day. Their system had no reporting or notifications, and there was no consistency between the forms in the system. The EHS manager would spend weeks searching through information to obtain the data needed for GPC’s annual Title V certification report and other reporting needs.
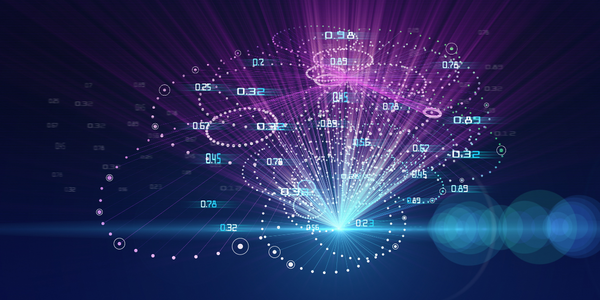
Case Study
Honeywell Enhances Data Quality and Efficiency with Locus Technologies
Honeywell, a Fortune 500 company specializing in diversified technology and manufacturing, was in need of an enterprise remediation data management system. The company sought a system that could safeguard and maintain the quality and integrity of their significant investment in generating site remediation data. They also wanted to ensure that this data was available for future use and could assure business partners of its reliable quality. Honeywell's existing data was scattered across stand-alone consultant systems, spreadsheets, and paper records, making it difficult to access and share within the company.
Case Study
Chevron centralizes data and streamlines data input and reporting with Locus’ EIM
Chevron, a leading integrated energy company, had various remediation sites spread out across multiple suppliers throughout the United States. They had no way of determining where their environmental data was or what condition it was in. They did not truly own the data that they paid for during remediation projects. Charges were incurred each time sites were transferred between consultants, and the quality and consistency of the data was not being managed properly. They needed a single repository to manage their data, unify reporting and streamline the process of generating data tables.
Case Study
San Jose Water Company automates and optimizes drinking water quality management and compliance data with Locus EIM Water software
San Jose Water Company (SJWC), a large water utility serving over a million people in the greater San Jose area, was in need of a more robust and comprehensive software solution for managing drinking water and general environmental compliance data. They were collecting routine and ad hoc samples from various activities and assets, and needed a solution to automate the entire process from sample planning to the preparation of regulatory reports. They also wanted robust data analysis tools to optimize their system operations and organizational performance, and integrated GIS to quickly view field and analytical data in real time.
Case Study
Reporting Effectively through SelfMade Mobile Applications
San Jose Water Company (SJWC) is a tech-forward company that manages dozens of internal and third-party applications. However, they faced challenges in managing their compliance programs and environmental recordkeeping. The regulations required recording company activities, which were not very predictable and involved diverse records to maintain. Before this effort, records were all managed on paper and in Excel, with no validation or backup. This made it difficult to ensure data accuracy and completeness. For example, the annual report for NPDES Discharge Reporting required hand-reviewing a full year's records, verifying data accuracy, entering it all into Excel, running analysis as required by permit, and formatting data for submission to the state.
Case Study
Honeywell achieves improves data quality, environmental risk reduction, and overall process cost reduction of over 50% with Locus’ EIM
Honeywell, a Fortune 500 diversified technology and manufacturing leader, was in need of an enterprise remediation data management system. The company required a system that could protect and preserve the integrity and quality of their substantial investment in generating site remediation data, have it available for future use, and assure business partners that legacy data is of reliable quality. Their existing data resided in stand-alone consultant systems, spreadsheets and paper records that was not readily available and shared within the company.
Case Study
GPC streamlines Clean Air Act Title V record keeping using Locus Platform
Grain Processing Corporation (GPC), a leading U.S. manufacturer of corn-based products, was struggling with an inefficient system for tracking and reporting compliance parameters for the Clean Air Act Title V. They were using SharePoint to enter over 20 daily logs at two facilities, with several questions per log and per shift, throughout a two-shift day. Their system lacked reporting or notifications, and there was no consistency between the forms in the system. The EHS manager would spend weeks searching through information to obtain the data needed for GPC’s annual Title V certification report and other reporting needs.
Case Study
Environmental Data Flow Six Sigma Process Improvement Savings Overview
The Environmental Data Flow Six Sigma improvement project was initiated in September 2009, driven by a cost-benefit analysis on data validation conducted earlier that year. The project aimed to improve LANL’s environmental data processing following receipt from the analytical laboratories. The project identified thirty-three process improvements, broken into seven subgroups. However, six of the improvements were never implemented, and two of the seven improvement subgroups did not lead to any cost savings but did lead to more accurate sample planning and increased transparency into the system.
Case Study
Del Monte effectively meets sustainability goals through improved data validation and customized reporting with Locus’ ePortal
Del Monte Foods, a large manufacturer and marketer of processed foods in the U.S., was struggling to meet its sustainability goals due to issues with data validation and manual report creation. The company was exporting data to spreadsheets to create reports, a process that was time-consuming and prone to errors. Del Monte needed a solution that would simplify reporting, ensure data quality, and make data more transparent within the company.
同类供应商.
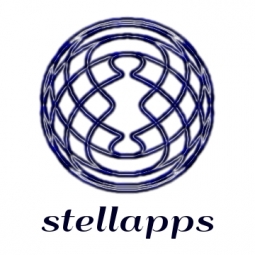
Supplier
Stellapps Technologies
Stellapps is an end-to-end dairy technology solutions company – the first of its kind in India. They are an IIT-Madras incubated company founded by a group of IITians and technologists with a strong industry background and rich experience including IIT-Madras, IIT-Kharagpur and IIM-Ahmedabad alumni, with over 18 years of Industry experience across Wipro, Nortel, Ericsson, Alcatel-Lucent, AT&T, Vodafone, Telstra, Bharti-Airtel, Aircel, Avaya, Cisco et al. Stellapps produce and procure comprehensive farm optimization and monitoring support, which helps dairy farmers and cooperatives maximize profits while minimizing effort. Stellapps is funded by Omnivore Capital – a fund anchored by Godrej Agrovet Limited and investment patrons include a large group of IIT alumni.
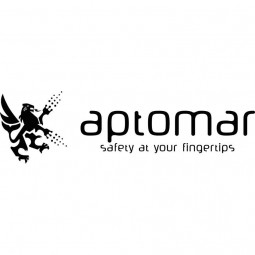
Supplier
Aptomar
Aptomar is a leading provider of Integrated Field Monitoring sensors, systems and services for the oil and gas industry. The company focuses on protecting the safety and integrity of people, the environment and assets by managing; 24/7 oil spill detection and combating, surveillance and security as well as search and rescue in close cooperation with Industry. Year founded: 2005

Supplier
Chatsworth Products
Chatsworth Products (CPI), an Anixter Technology Alliance Partner, is a global manufacturer providing voice, data and security products and service solutions that optimize, store and secure technology equipment. CPI Products offer innovation, configurability, quality and value with a breadth of integrated system components, covering virtually all physical layer needs.
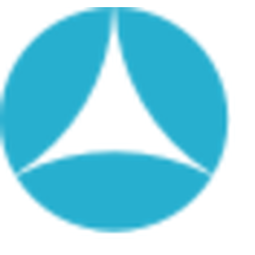
Supplier
Connexxs
Connexxs is the forth in a line of companies founded, managed or coordinated by Connexxs executives. Our first company grew from a need we saw in the operations of large natural gas fired cogeneration plants we developed. In those plants we needed an automated means to know how much gas we had available to use during each day and on what pipeline it would be delivered, if called upon.From the cogeneration experience we co-founded a company that now remotely monitors over 6,000 natural gas compressors throughout the US and Canada. This company uses both the cell data networks and satellite communications to provide its customers with the best service at the lowest costs.