Advantech
启用智能星球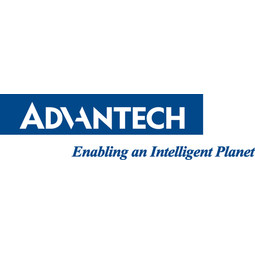
概述
总部
台湾
|
成立年份
1983
|
公司类型
上市公司
|
收入
$1-10b
|
员工人数
1,001 - 10,000
|
网站
|
股票行情
TPE: 2395
|
推特句柄
|
公司介绍
Advantech 成立于 1983 年,是提供值得信赖的创新嵌入式和自动化产品及解决方案的领导者。研华提供全面的系统集成、硬件、软件、以客户为中心的设计服务和全球物流支持;所有这些都以行业领先的前台和后台电子商务解决方案为后盾。
物联网解决方案
研华一直是开发和制造高质量、高性能计算平台的创新者。他们与我们的合作伙伴密切合作,帮助为各行各业的各种应用提供完整的解决方案。为实现我们的企业愿景,打造智能星球,研华将继续在智慧城市和物联网解决方案方面开展合作和合作。
子公司
物联网应用简介
Advantech 是基础设施即服务 (iaas), 平台即服务 (paas), 应用基础设施与中间件, 分析与建模, 功能应用, 网络安全和隐私, 网络与连接, 处理器与边缘智能, 传感器, 自动化与控制, 和 可穿戴设备等工业物联网科技方面的供应商。同时致力于农业, 服装, 汽车, 建筑物, 建筑与基础设施, 电子产品, 设备与机械, 食品与饮料, 医疗保健和医院, 金属, 可再生能源, 零售, 半导体, 运输, 和 公用事业等行业。
技术
用例
功能区
行业
服务
技术栈
Advantech的技术栈描绘了Advantech在基础设施即服务 (iaas), 平台即服务 (paas), 应用基础设施与中间件, 分析与建模, 功能应用, 网络安全和隐私, 网络与连接, 处理器与边缘智能, 传感器, 自动化与控制, 和 可穿戴设备等物联网技术方面的实践。
-
设备层
-
边缘层
-
云层
-
应用层
-
配套技术
技术能力:
无
弱
中等
强
Supplier missing?
Start adding your own!
Register with your work email and create a new supplier profile for your business.
实例探究.
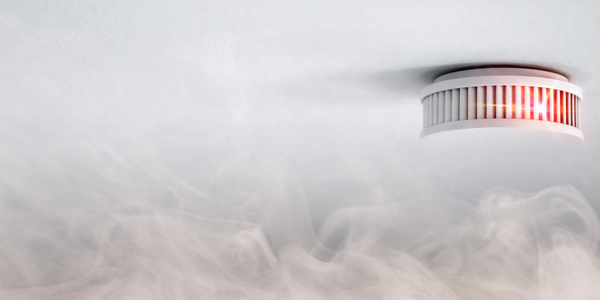
Case Study
Fire Alarm System and Remote Monitoring Sytem
Fire alarm systems are essential in providing an early warning in the event of fire. They help to save lives and protect property whilst also fulfilling the needs of insurance companies and government departments.Fire alarm systems typically consist of several inter-linked components, such as smoke detectors, heat detector, carbon monoxide, manual call points, sounders, alarm and buzzer. The fire alarm system should give immediate information in order to prevent the fire spread and protect live and property.To get maximum protection a shoe manufacturer in Indonesia opted for a new fire alarm system to monitor 13 production sites spread over 160 hectars. Although the company had an existing fire alarm system, it could not be monitored remotely.It was essential that the new system would be able to be monitored from a central control room. It needed to be able to connect to the existing smoke detector and manual call point. Information should be easily collected and passed on to the Supervisory Control and Data Acquisition (SCADA) system. Furthermore, the system should have several features such as alarm management, auto reporting, being connected to many client computers without additional cost, and run 24/7 without fails. The company also needed a system which could be implemented without changing the architecture of the existing fire alarm system.
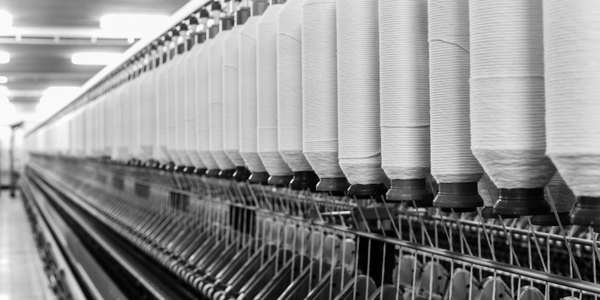
Case Study
IoT Applications and Upgrades in Textile Plant
At any given time, the textile company’s manufacturing facility has up to 2,000 textile carts in use. These carts are pushed from room to room, carrying materials or semi-finished products. Previously, a paper with a hand-written description was attached to each cart. This traditional method of processing made product tracking extremely difficult. Additionally, making sure that every cart of materials or semi-finished products went to its correct processing work station was also a problem. Therefore, the company desired an intelligent solution for tracking assets at their factories. They also wanted a solution that would help them collect process data so they could improve their manufacturing efficiency.
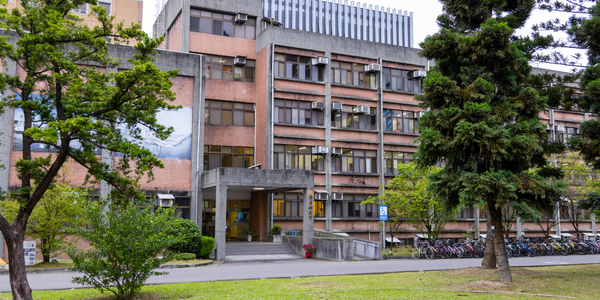
Case Study
Energy Saving & Power Monitoring System
Recently a university in Taiwan was experiencing dramatic power usage increases due to its growing number of campus buildings and students. Aiming to analyze their power consumption and increase their power efficiency across 52 buildings, the university wanted to build a power management system utilizing web-based hardware and software. With these goals in mind, they contacted Advantech to help them develop their system and provide them with the means to save energy in the years to come.
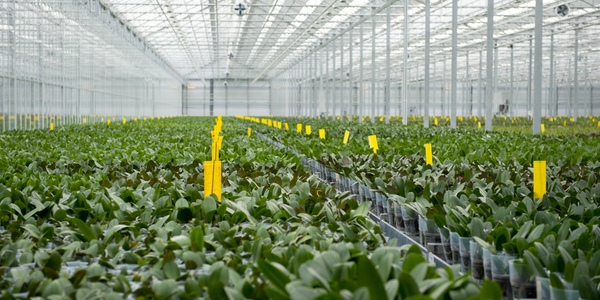
Case Study
Greenhouse Intelligent Monitoring and Control Solution
Farming Orchids is the most successful form of precision farming in Taiwan, and also the most exported flower. Orchids need a specific temperature and humidity conditions to grow and bloom, and its flowering time may not be in line with market demands, so the price collapses when there is overproduction. Therefore, some farmers began to import automated greenhouse control systems for breeding and forcing, which not only improves quality, but also effectively controls the production period and yield to ensure revenue. In 2012, an orchid farmer built a Forcing Greenhouse of about 200 pings (approximately 661 Square Meters) in Tainan, Taiwan. The system integrator adopted Advantech’s APAX-5000 series programmable automation controllers to build the control platform, coupled with Advantech WebAccess HMI/SCADA software, to achieve cloud monitoring. The staff of the orchid field can monitor important data anytime via smart phone, iPad, and other handheld devices, and control the growth and flowering conditions. System requirements: In the past, most environmental control systems of orchid greenhouses in Taiwan used PLCs (Programmable Logic Controller) with poorscalability and control, and could not be connected to the Internet formonitoring from the cloud. For advanced database analysis and networking capability, the PC platform must be adopted. Therefore, PAC Systems (Programmable Automation Controller) with both PLC programming capabilities andPC functions is a better choice.The environmental control of the Orchid greenhouse switches on and off devices like fan, shade net, cooling/heat pump, liquid flow control, water-cooling wall etc. It is controlled by a control panel of electric controllers, and is driven by a motor, to adjust the greenhouse temperature, humidity, and other environmental conditions to the set parameters.
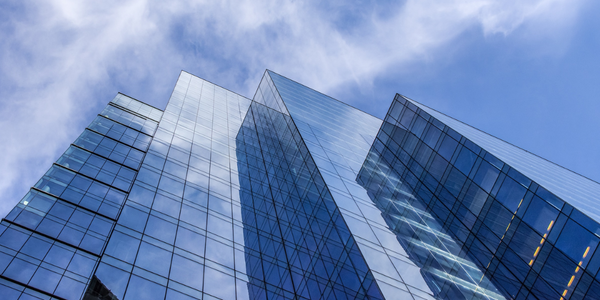
Case Study
Intelligent Building Automation System and Energy Saving Solution
One of the most difficult problems facing the world is conserving energy in buildings. However, it is not easy to have a cost-effective solution to reduce energy usage in a building. One solution for saving energy is to implement an intelligent building automation system (BAS) which can be controlled according to its schedule. In Indonesia a large university with a five floor building and 22 classrooms wanted to save the amount of energy being used.
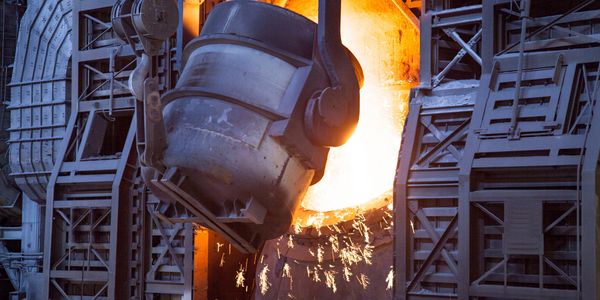
Case Study
Continuous Casting Machines in a Steel Factory
With a very broad range of applications, steel is an important material and has been developed into the most extensive alloy in the engineering world. Since delivering high quality is absolutely crucial for steel plants, ensuring maximum productivity and the best quality production are the keys to competitiveness in the steel industry. Additionally, working conditions in steel factories are not suitable for workers to stay in for long periods of time, so manufactures usually adopt various machines to complete the steel production processes. However, the precision of these machines is often overestimated and the lack of flexibility also makes supervisors unable to adjust operating procedures. A renowned steel factory in Asia planned to improve its Distributed Control System (DCS) of furnaces as well as addressing the problem of insufficient accuracy. However, most well-known international equipment suppliers can not provide a satisfactory solution and local maintenance because the project needed new technologies to more accurately control equipment operations. By implementing Advantech’s automated monitoring and control solution, steel factories can not only improve the manufacturing processes but can also allow users to add additional functions to the existing system so as to make sure the operation runs at high efficiency.

Case Study
Monitoring and Controlling Automatic Mixing and Dispensing Machines
As technology advances, textile manufacturing has been transformed from a labor-intensive to a partially or fully automated industry. Automation is significant in all segments of textile production - from spinning to printing, and textile machinery manufacturers are constantly searching for new technologies and automation processes will increase the productivity of their machines. The color paste mixing and dispensing machine is an essential part of the printing and dyeing process. With the advantage of automatically computerized controls and database management, the system can significantly improve its dispensing precision, working efficiency and production quality as well as reducing material consumption.
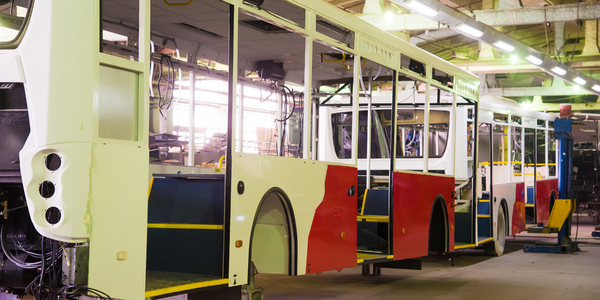
Case Study
Bus Manufacturers to Realize a Smart Factory
China's Yutong Bus Group is a large-scale manufacturing company. Its enterprise scale and sales performance continuously ranks first in the nation’s bus industry, and its bus products are exported to more than a hundred countries and regions. In order to improve the manufacturing process and carry out the transparent production control, the company planned to upgrade the existing manufacturing floor into the advanced and efficient factory. In addition to using MES as the production management system, it was also necessary to adopt panel PCs as the HMI and to establish a network communication in the manufacturing site. On account of stability, the IT department of this company excluded commercial computers and decided to choose the industrial product which has the advantages of high-performance and low failure rates. The factory is a complex and harsh environment, so this project required providing different kinds of panel computers with rugged features for different machine uses, offering wired and wireless network devices to create a complete communication link, and the related modules to acquire peripheral data. Therefore, to ensure this stability, the system integrator used industrial grade wireless devices with wider network coverage and higher power output.
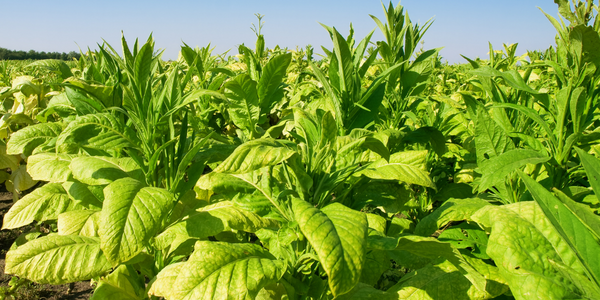
Case Study
Controlling and Monitoring Tobacco Plants in China
Without the aid of computers, calculating production volume in a tobacco plant is troublesome and error-prone. PC-based monitoring systems that automatically collect production data and keep records can greatly improve in-factory logistics management and machinery maintenance. Combined with the use of networking communications, a Manufacture Executive System (MES) can be developed to improve the overall management of the factory. Our customer is a branded tobacco producer in China. When they came to Advantech, their production lines were already automated with the deployment of Programmable Logic Controllers (PLCs). However, they were still dependent on manual labor to count the amount of cigarettes and other materials, and their engineers had to manually check and record the data-logs stored in the PLCs to produce analyses for repair and maintenance purposes. But with Advantech’s PC-based monitoring machines, installed next to manufacturing machines, related data is shown on touch screens and transmitted to the control center, helping to reduce errors and improve management efficiency.
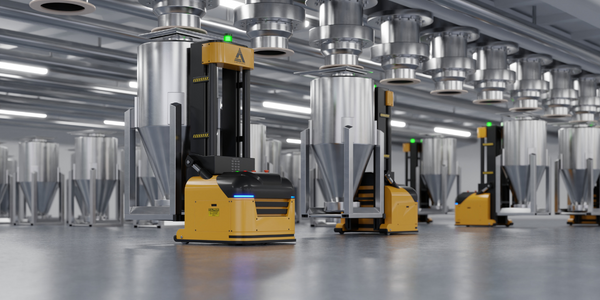
Case Study
PC-based PAC solution for material handling AGV optimization
Widely used across many industries, Automated Guided Vehicles (AGV) have been scooting around factory floors for decades. Thanks to evolving technologies like sensors, wireless networks and automatic control technologies, their guidance methods and physical dimensions continue to evolve and now small lightweight trackless AGV are being rolled out. An American AGV System Integrator (SI) was designing a Laser Guided Vehicle (LGV) for a material handling system in an automotive assembly plant. Since the plant’s existing AGV system used an expensive PLC-based control system there weren’t enough functions to meet the new control requirements, the company decided to upgrade and shift to a compact PC-based PAC control system ideal for the new compact vehicle design, capable of integrating with upper management systems using a single software application to replace the original two software applications.
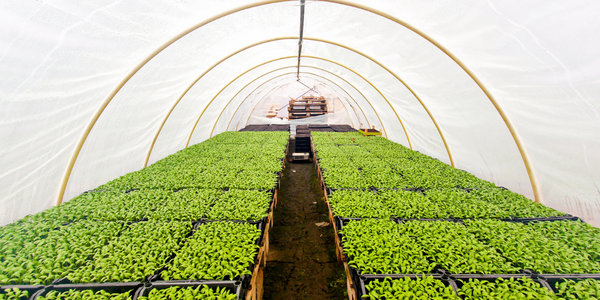
Case Study
Remote Monitoring and Controlling of Greenhouses
For people who live and work in big cities, growing their own fruits and vegetables is a dream which is often difficult to realize. But how about renting a greenhouse, and being able to remotely plant seeds, spray water and apply fertilizers through a webpage, and then watching how your crops are growing via streaming video from an IP camera while you occasionally pay a physical visit to your plants at the weekends or holidays to harvest and cook your vegetables at a feast? A group of young Taiwanese entrepreneurs are making their own, and other people’s dreams come true by establishing greenhouse plots for rent. Leveraging the latest Advantech technologies and features provided by the ADAM-6200 series Ethernet I/O series and WebAccess 8.0 HMI/SCADA software, they’ve created a greenhouse automation and remote monitoring solution from which their customers can control and monitor the environment via a virtual dashboard on a computer, smartphone or other web-based device in real time.
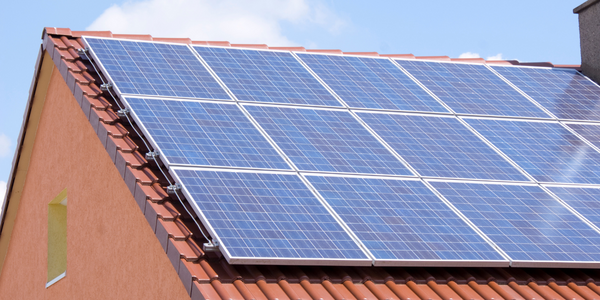
Case Study
Real-time Monitoring and Unified Management Platform for PV Plant
As PV power plants continue to increase, centralized management and information integration become thorny problems.Enterprise PV systems mainly supply power for their own needs and may sell excess power to the power company whereas Photovoltaic (PV) power plants specialize in solar energy collection and then feeding the energy into the grid.To transmit the data of the PV systems wired or wireless networks can be used. However, wireless networks have the advantage of flexibility and are the best choice for those who want quick deployment.Taking into account the requirements of wider coverage and long-distance transmission, the existing fiber-optic networks had many shortcomings ie high cost, complicated wiring and long construction period, and it may also have been necessary to excavate walls, drill holes, embed wires, or even destroy the original building structure. After evaluation, the Juli Group decided to adopt an easy installation and easy expansion wireless network system for early completion of this project.
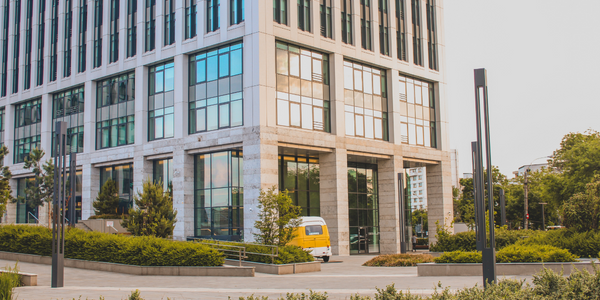
Case Study
Energy Conservation and Efficiency in a Shanghai Office Building
Conservation of energy resources through energy management solutions are receiving considerable attention in the modern office building sector. Specific questions were directed towards average monthly energy costs and energy consumption. Meanwhile administrators need to have sufficient information about the state of their facilities’ to plan energy conservation. For those reasons, new office buildings are usually embedded with advanced technology energy efficiency features to monitor their electricity and water resources to detect leaks in the building’s plumbing and facilities usage to reduce energy costs as well as providing a comfortable office environment.
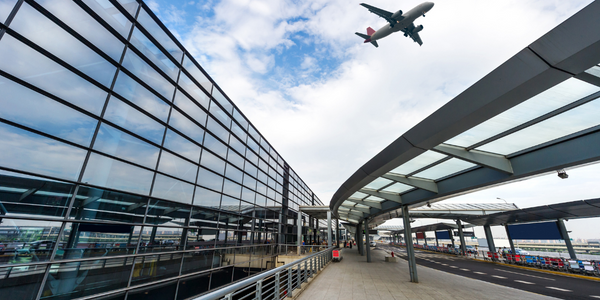
Case Study
Advantech’s Flight Information Display Systems Take Off at Airport in China
Improve infrastructure efficiencyProvide a solid foundation for remote management technology used in Advantech’s Flight Information Display System (FIDS), rapid provisioning and optimal use of all computing resources.Reduce operational costsEnable customers to reduce time and manpower costs in discovering, healing, and protecting their networked computing assets.
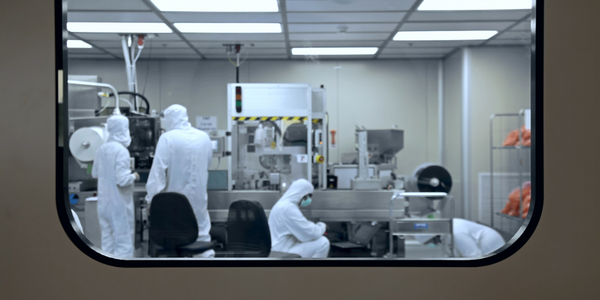
Case Study
ThinManager Ready Solutions for Factory Management
A medical product company needed to install 230 thin client PCs across four manufacturing plants. Thin clients have been used in offices for many years, but their introduction onto the factory floor has been slow. A thin client network consists of a management computer in a secure, air-conditioned room with back up UPS, whilst on the factory floor there are a number of simple computers which are used to connect to the management computer, thereby removing the need to install individual operating systems and applications on each of the clients whilst also ensuing that there is only one point of failure.The company was looking for a network architecture that would have the lowest maintenance costs and the quickest deployment time. To meet all these needs, each of these sites would have approximately 50 thin clients installed on the factory floor and these would then be connected to a central server located elsewhere on the site. This leaves only one point of maintenance for software updates, security patches and rules for what applications are allowed to run on the thin clients.

Case Study
Human–Robot Control
Industry 4.0 is changing the way manufacturing industry operates. Increasingly more manufacturers are leveraging advanced technologies such as robotics and automation systems to improve productivity and efficiency. As a result, human–machine interfaces (HMIs) are becoming more important in their role in the digital connectedness of humans and machines. However, using the wrong HMI can lengthen development times and increase implementation costs.
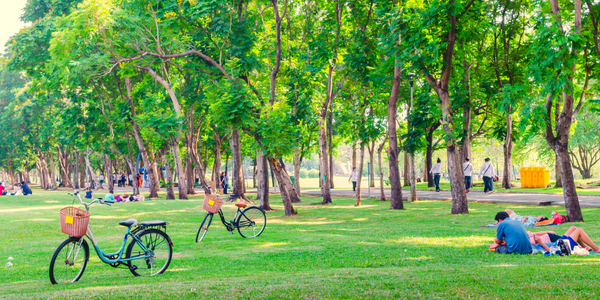
Case Study
Improving Building Comfort and Energy Savings
During the energy crisis of the 1970’s there was a sea-change in the building industry when it paid more attention to the idea of conserving energy and introduced the terms Building Management System (BMS) and Building Automation System (BAS). Continuing rising energy prices and carbonreduction issues have also further spurred the development and deployment of BMS in recent years. However, the early systems were bulky, not user friendly, unreliable, and very expensive. With the advent of computerization, BMS analog signals became digitized so as to be communicated over long distance as well as facilitating the building management process these issues became less.Due to the multiple many management functions and wide range of expertise, modern BMS is quite complex. Successful building management not only needs to link to a multitude of devices but also take account of the suitability of the software for the intended application. Equipped with a web browser-based software package for human-machine interfaces (HMI) and supervisory control and data acquisition (SCADA) which provides automated, centralized and unattended management with a high degree of electronic accuracy, the BMS can fully control the building’s mechanical and electrical equipments and thus effectively monitor energy consumption so that it provides a comfortable, safe and secure environment.Property management is facing various and complex challenges and reducing operating costs have become increasingly important for building owners. As a result, a growing number of new and refitted buildings are being designed to use less energy and focus on the building’s performance. A System Integrator was helping a builder implement advanced BMS for its newest construction project in a creative park in Asia. The construction, a 14-storey building with four underground floors, covers an area of nearly one hundred thousand square meters and contains three distinct sectors - shopping mall, hotel guest room floors and office floors. In order to provide optimal energy management, this BMS needed to be capable of monitoring and controlling a variety of facilities, including air conditioning, power system, plumbing system, fire system, ventilation, elevator, lighting, garden watering and so on. Meanwhile, using one system with an adequate number of nodes in a main control room to manage three different places was a key requirement but each place had to have their own dedicated system and can be controlled independently without mutual interference so as to saving the implementation costs. Due to the need to monitor many areas, there would be tens of thousands of detection points, and the new system also needed to offer remote control capabilities so that building managers or patrol staff can view the status of various facilities in real-time and deal with issues using handheld or mobile devices.
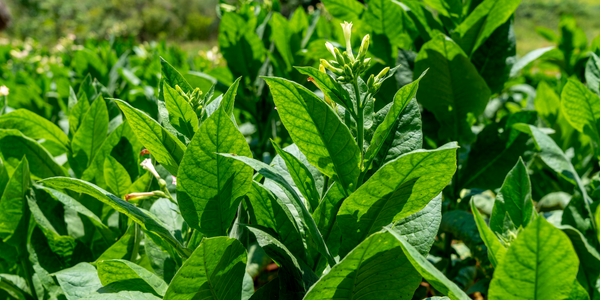
Case Study
Smart Factory Solutions for Tobacco Industries: Bridging the Manufacturing Generation Gap and Improving Operational Efficiency
The tobacco industry, represented in this case by British American Tobacco (BAT), is facing a decline in cigarette volumes worldwide. This decline has led to an increased emphasis on efficient supply chains and optimized production processes. The industry is also grappling with the need for agile production facilities and the integration of Industry 4.0 to accommodate diverse production requirements. BAT, in particular, was seeking a factory solution to automate their product control processes, from the transportation of tobacco and cigarette paper to the placement on cigarette machines and the packing conveyor. The company also needed to support the continuous use of legacy equipment, such as relay-controlled cigarette machines dating back to the 90s and AMK servo drive systems, to sustain production levels at speeds of 8000 to 16000 pieces per minute. Furthermore, changing regulatory guidelines necessitated flexibility in labeling requirements.
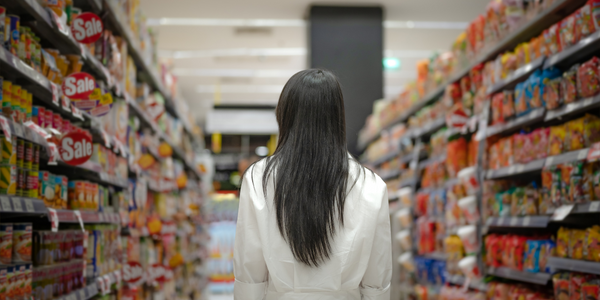
Case Study
Convenience Store Energy Saving Application
Since electricity costs keep on rising, the bills for convenience stores keep on increasing and unfortunately it’s difficult for convenience stores to raise their prices to maintain the same profit margins. Variable overheads are difficult to budget for and give accountants a headache, therefore one convenience store chain in Thailand has decided to redress the balance and put themselves in chargeof power generation by installing solar panels in their stores.Our customer wanted to reduce their energy costs by at least 10 percent and having installed solar panels in their store locations they needed to be able to send the power to where it was needed and when it was needed. Since the stores are open for 24 hours and it’s onlysunny forroughly 12 of those, it was essential that the power distribution to the lighting and refrigeration units was managed efficiently.
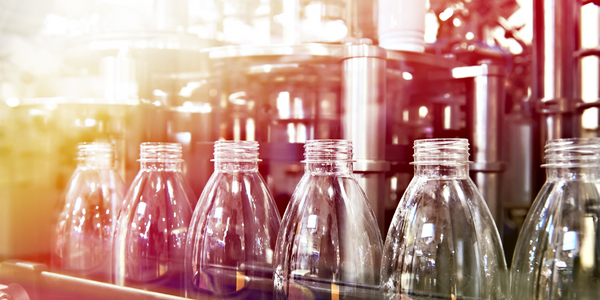
Case Study
Automatic Vision Inspection Solution for Product Traceability
With greater market demand for food safety, traceability is receiving increasingly more attention in the food and beverage industry as well as the packaging industry. One of the world's leading providers of beverage containers required a system to identify bar codes and alphanumeric characters on ink-jet-printed labels at a run rate of 7 units and minimum 99.9% accuracy. Since there were few engineers in the factory, the customer sought to implement a reliable system with an easy-to-use GUI for workers with a less technical background.
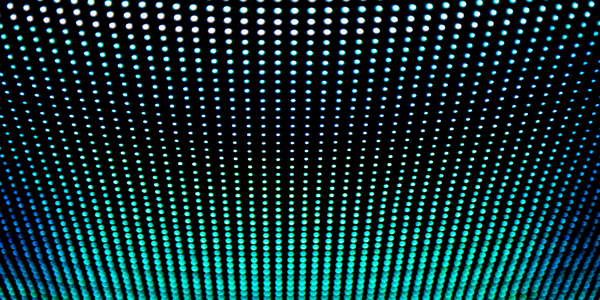
Case Study
A FOG Vision Control Solution for an LED Module Production Line
This manufacturer of LED module bonding machines was in the process of developing large vision machines that comprised 17 industrial PCs (IPCs) in a single machine.They had been testing several IPC brands to identify the ideal one that would improve the stability of their machines. Given the number of IPCs in each machine,having compact IPCs was a major priority for their project.
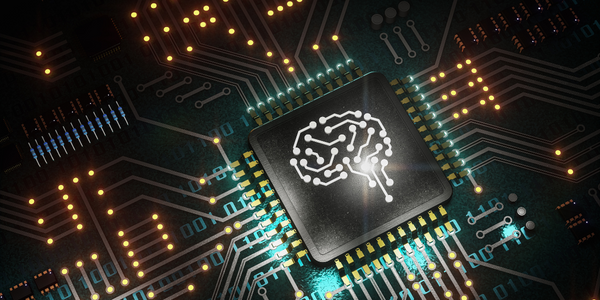
Case Study
Modular AI Defect Inspection Solution for Efficient Semiconductor Equipment Upgrades
Smasoft Technology Co., Ltd., a System Integrator that develops industrial automation software and offers AI application solutions, was commissioned by a semiconductor equipment manufacturer to implement AI inspection features into their Extreme Ultraviolet Light (EUV) pod inspection machines. The existing AOI software in the EUV pod inspection machines could only identify defective products but could not trace the cause of the defects. The manufacturer wanted to upgrade their machines with AI features to make the products more useful. The AI solution needed to complete the analysis of 380 images for a single pod within two minutes and inspect different materials simultaneously. This required multiple sets of AI models for interpretation. The solution also needed to be installed in a cabinet in the lower half of the machines, which posed a challenge due to the limited space. Smasoft needed to purchase a hardware solution with strong computing performance, stable operation, compact size, and flexible configuration to overcome these challenges.
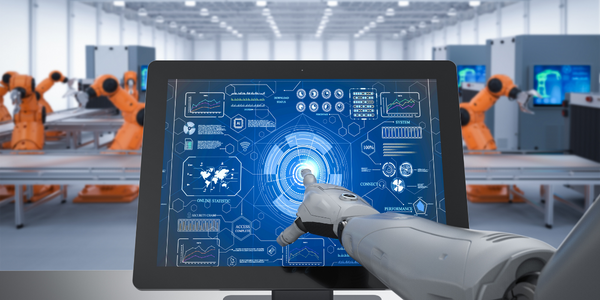
Case Study
HMI Total Solution Enables Bus Manufacturers to Realize a Smart Factory
Industry 4.0 is gradually becoming a reality, and manufacturers are actively transforming their production process into intelligent manufacturing systems by leveraging Information Technology (IT) and Operations Technology (OT).The main concept of Industry 4.0 is to realize transparent vertical and horizontal integration from the production line to management level so as to increase productivity and efficiency. In other words, the resources available throughout the entire production process must be digitalized and networked so that they can be visible and completely availability.
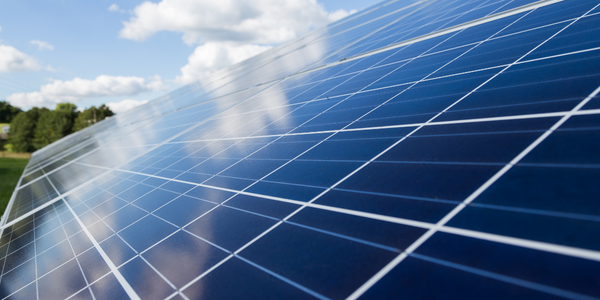
Case Study
Smart Monitoring Solutions for Solar Panels: A Case Study
In 2018, the Japanese government approved the Fifth Energy Basic Plan, prioritizing renewable energy and setting it on a course to become the primary power source in Japan. This led to the re-introduction of solar panels as a renewable energy source. However, renewable energy sources such as solar power have weaker 'bearing capacity' than other power generation methods due to their characteristics. Solar power can be challenging to control because the output fluctuates based on weather conditions. If a large amount of electricity is supplied from the photovoltaic power generation sources to the grid when the power demand is low, the voltage and frequency can be disturbed, and the entire grid can become unstable. In some cases, it can lead to a large-scale power outage. This risk necessitated developments to solve problems like monitoring and controlling the amount of electricity produced by solar panels. NWC partnered with a client that generates and sells electricity serving residential, commercial, and industrial customers. The client needed to monitor the amount of electricity produced by 88,000 solar panels with a power generation capacity of 28 MW/h in a field size of 700 x 700 meters. The initial idea was a 13 kilometer wired optical network; however, the cost of over 1 billion yen made this approach expensive and impractical.
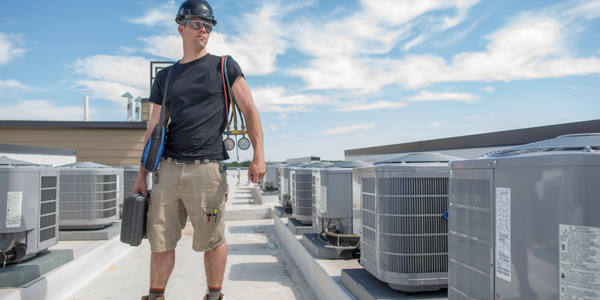
Case Study
Edge Solutions for Smart Monitoring of HVAC Manufacturing: A Case Study on Daikin India
Daikin India, a leading HVAC solutions provider, was seeking to optimize energy efficiency and productivity at its factories. The company wanted to implement an equipment monitoring and data collection solution for its HVAC subassembly lines. However, the challenge was that these lines featured numerous programmable logic controllers (PLCs), which limited the available installation space and network capabilities. Therefore, Daikin India needed a compact yet versatile solution for acquiring and visualizing production data without high networking/infrastructure costs. The company also required a system that supports smart real-time monitoring of HVAC subassembly lines, enables seamless acquisition and visualization of equipment data, minimizes and streamlines data transmissions, offers configurable PLC I/O data collection flexibility, and provides reliable industrial-grade hardware.
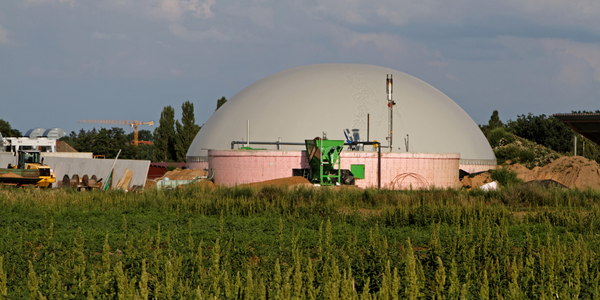
Case Study
Smart Monitoring System for Taiwan's First Micro-Biomass Power Plant
SunForce Technology Co., Ltd was tasked with developing a monitoring system for micro biomass power plants in Taiwan. The goal was to reduce labor expenses and equipment failure rates while increasing power generation. The challenge was to create a system that could perform scheduling and cascade control to create standard operating procedures. The aim was to achieve remote monitoring and real-time management of the power plants. The system was also expected to adapt to third-party software and interface with environmental protection authorities, as well as export biomass electricity for sale to Taipower. The future plan was to combine artificial intelligence with gradually accumulated operational data to perform intelligent monitoring.
Case Study
Advantech SRP-FPV240 ThinManager® Solution, Greater Quality Assurance for Enhanced Productivity
The pharmaceutical industry is heavily regulated, and manufacturers must maintain strict quality controls to ensure the safety of their products. One producer of pharmaceutical packaging was experiencing the costs of outdated production processes firsthand. With four manufacturing sites to manage, corporate headquarters found the remote process increasingly unsustainable. The manufacturer required a means of centralizing the management of all process visualization applications so that key adjustments could be performed remotely at its headquarters, thus saving on the firm’s limited IT resources while still ensuring the required traceability and regulatory compliance.
Case Study
Kapsch CarrierCom* and Advantech* Use NFV to Deploy Universal CPE
The majority of network functions can now be hosted on Intel architecture-based servers. This has led to the expanded use of virtualized universal customer premises equipment (uCPE) networking systems that can deliver branch office networking functions with the capacity for additional virtual network functions (VNFs) that let communications service providers (CommSPs) deploy custom, value-added services. Kapsch CarrierCom, a global producer, supplier, and systems integrator of end-to-end telecommunications solutions, chose Advantech as its CPE hardware vendor, and together they have developed a comprehensive network customer deployment solution leveraging software contributions from an ecosystem of software vendors, including Cloudify, the TOSCA-based provider of management and orchestration (MANO).
Case Study
Enhancing Customer Experience with Rugged and Stylish Wayfinding Kiosks
Xiaomeisha SeaWorld, one of the biggest aquariums and theme parks in China, aimed to enhance visitor experience by installing interactive wayfinding kiosks in its eight exhibition buildings. However, the original kiosks, composed of a 32" touchscreen and a digital signage box, malfunctioned due to the high humidity in the aquarium. Moreover, the kiosks broke after only a few months of use. Therefore, the customer decided to look for a more rugged and attractive replacement kiosk solution that could provide stable operation in heavy-duty and high humidity environments, reflect SeaWorld’s premium image, and run interactive software smoothly.
Case Study
Waste Management Solution Enables Accurate Real-Time Data Reports in Lima, Peru
The city of Lima was looking for a fleet management solution that would facilitate the city’s garbage truck fleet monitoring and waste management operations. They needed an in-vehicle solution that could monitor vehicle movements, diagnostics, and, crucially, driver behavior. The customer required the ability to log driver behavior and routes to ensure compliance with city safety regulations. The system’s power supply, shock resistance, and core temperature range should be suitable for operation in harsh environments. In-vehicle computers should conform to several special requirements. For example, older trucks tend to have an unstable power supply, excessive noise, and insufficient voltage, which hinder system activation. When connected to peripheral devices, a sudden voltage surge can damage the motherboard, and bumpy roads may cause power outages or computer failures. Moreover, systems without a wide operating temperature range cannot perform consistently in extremely hot or cold weather.
Case Study
SetiBT Long-Distance Fueling Project
SetiBT, a specialist IT services provider based in Brazil, was approached by a large fuel and lubricant transportation company for an in-vehicle fuel transportation solution. The company operates a substantial fleet of tankers that supply fuel to remote locations such as sugarcane processing plants, construction sites, and mining operations. The challenge was to manage the fuel loading processes for specialist equipment in the field, inhibit fraud and fuel theft, and increase the accuracy of data acquisition to better control costs. The system also needed to be capable of automatically identifying the equipment being fueled, including tank size and type of fuel required, as well as synchronizing with the vehicle’s horometer, odometer, and GPS. These functions would offer a clear breakdown of each vehicle’s productivity, status, and risk, thereby providing customers with accurate data to increase efficiency and reduce costs.
Case Study
CPC Corporation Improves Operational Efficiency with Advantech’s ABox Solution
CPC Corporation, Taiwan's leading enterprise in the development and supply of petroleum and natural gas, faced a challenge in ensuring operational efficiency in semi-outdoor environments. The company needed a high-performance POS system that could withstand environmental challenges associated with gas stations, including resistance to water, dust, shock, and oil. Additionally, the company needed to protect their customer database from unauthorized employee access, making traditional POS systems inappropriate.
Case Study
Self-Service Price Check System Enables Real-Time Price Inquiries for Hypermarket Chain
The hypermarket industry is intensely competitive, and satisfying customer demands and increasing brand loyalty are the primary business challenges for Far Eastern A.mart. To increase customer loyalty, Far Eastern A.mart planned to establish loyalty programs that encourage increased purchasing. They wanted a wall-mountable POS system that could be used to check product prices and customer reward points in real-time to enhance the overall service quality.
Case Study
Supply Chain Management in the Automotive Industry
The automotive industry is characterized by high quality expectations, product variety, and process complexity. Globalization and increasing customer requirements have forced car manufacturers to offer a large range of vehicle models and options. This complexity, coupled with the pressure of international competition, makes efficient logistics a challenge. The industry also faces the challenge of ensuring that a vast variety of car components supplied by various sources in different countries is delivered to the production plant on time. This requires well-engineered mobile computing solutions. Another challenge is the just-in-sequence production principle, which requires the delivery of the correct individual automotive parts to every workplace in the production line, in the exact sequence in which the vehicles are being assembled.
Case Study
Nippon Valqua Industries, Ltd. Case Study
Nippon Valqua Industries, a leading manufacturer of industrial packing and gaskets, faced the challenge of extending the service life of weld bellows. The bellows consist of an accordion-folded frame formed with elaborate metal disks cut out of corrugated plates, of which the inner and outer edges are alternately welded. The welded bellows have elastic and airtight features and are applied for seal application, such as ultra-high vacuum valves for the semiconductor industry, wafer processing equipment and single-crystal grower, as well as gyroscopes, accumulator and dampers used for aerospace vehicles. To extend the service life, it was critical to optimize the shape of corrugated plates comprising welded parts. For the design of welded bellows that receive concentrated reaction force on/around welded parts, it was critical to create a corrugated plate best suited to disperse such concentrated reaction force.
Case Study
YCM Turns to Advantech to Co-Create a CNC Management Solution for Intelligent Metal Manufacturing
China’s metal manufacturing industry faces numerous challenges, including a lack of standardized communication interfaces, low-level intelligence in existing equipment, and a low level of informatization in existing systems. YCM, a leader in machine tool manufacturing, is not exempt from these challenges. With the advent of Industry 4.0 and new trends in IoT, YCM faces huge challenges in making their manufacturing smarter using digitized information and visualized data intelligence. Rapid changes in the marketplace, emerging market competition, limited resources and sustainability, slow growth, labor shortages and transitioning business integration are common problems in China’s metal manufacturing industry. To overcome these challenges, YCM needed to focus on process management that yields decreased time-to-market while delivering high-quality and competitive product pricing.
Case Study
Impelex and Advantech Transform the Metal Processing Ecosystem with iFactory SRP
RE-DAI Precision Tools, a leading hand tool manufacturer in Taiwan, was facing significant challenges due to its traditional industrial manufacturing and management model. The company had a diverse portfolio of production machinery acquired over the years, which led to a haphazard approach to managing the machinery. The challenge for Impelex was to implement a real-time system that monitored machine operations and incorporated a mobile dashboard to prevent power outages and improve overall production efficiency. RE-DAI needed a fully mature communication solution to unify and control all the disparate systems on one platform.
Case Study
Nippon RAD and Advantech Transform Japan’s Industry 4.0 Centric Solutions
Nippon RAD, a long-established IT system integrator in Japan, identified a significant challenge in the country's automotive industry. Many auto component manufacturers were struggling to effectively collect and visualize machine data from production lines, especially from different machines, purchased from different suppliers, each with multiple protocols. With an expanding portfolio of multi-branded production machinery acquired over a prolonged period of time, manufacturers felt unable to properly meet the challenges of increased competition and change management. The lack of real-time connectivity between people, machines, and devices, as well as information and communication technologies for the dynamic management of the ever-increasing complexity of the business process, was a major issue.
Case Study
How Advantech’s Innovative Solutions Are Advancing Manufacturing in Thailand
In Thailand’s export-oriented economy, manufacturing is the primary driver of economic development and growth. However, globalization provides increasing opportunities to sell Thai products around the world, it also fosters fierce competition between rival companies. In this ever more competitive market environment, manufacturers must leverage every innovation available to maximize the value and efficiency of their production lines. Yet, most factories in Thailand have limited space for new equipment. Facilities also vary widely in terms of environmental conditions and the ease of adding new cabling. Moreover, with limited margins leaving little funding for infrastructure investments, most Thai manufacturers cannot afford to even replace existing equipment. Considering these constraints, an effective equipment monitoring system must be sufficiently compact and flexible to allow installation in diverse factory environments and to support a wide range of machinery and equipment.
Case Study
Simple Process Visualization Solutions for Automotive Production Lines
The production lines of a Japanese auto parts manufacturer required cutting-edge precision and coordination. The company faced a specific problem hindering the coordination of their production lines; namely, the inability to efficiently collect and visualize data from their FANUC CNC machines. The company needed a means of easily collecting and displaying data on power and air consumption as well as grinding wheel wear, which were to be used for machine analysis. However, the manufacturer’s in-house operations and IT engineers lacked the time and knowledge to establish an effective strategy.
Case Study
Smaller is Better: Production Management Solutions for Greater Manufacturing Precision
A semiconductor equipment manufacturer in Korea was facing issues with their production line monitoring and management. The existing system lacked important capabilities needed for efficient data collection, visualization, and utilization. Individual line workers had no means of quickly reporting production problems, and important information regarding the problems that did occur often went unrecorded, allowing them to reoccur with unacceptable frequency. The company’s most critical need was ensuring the ability to collect, visualize, and utilize critical data as quickly and efficiently as possible.
Case Study
Software and Hardware Integration Delivering Key Precision Solutions
The EMS company's clients were facing a challenge with their production line machines. Although various sensors collected critical data from these machines, the data was not consolidated in the cloud nor visualized to facilitate critical improvements to the production line and prevent costly interruptions. The company needed a solution that could provide seamless data integration and visualization to optimize production efficiency and preemptively maintain the machines to prevent unexpected system downtime.
Case Study
Manufacturing Made Smarter: How Advantech’s Machine Data Acquisition Solutions Take Manufacturing to the Next Level
The home appliance manufacturer in Thailand was facing challenges in tracking productivity and key parameters of the process. In modern manufacturing, production lines for different types of products share certain fundamental commonalities. By actively managing production line assets, manufacturers can ensure that production is optimized. However, the data provided by various production line assets is sometimes contradictory or unclear due to the sensors, meters, or PLC controllers being limited in connectivity or because different devices from different vendors may each have their own proprietary protocols.
Case Study
Driving the Future: How Advantech’s Innovative Solutions Are Spurring the Evolution of Manufacturing in Indonesia
The Indonesian manufacturer, a leading provider of key solutions to corporate partners worldwide, was seeking to enhance its production line efficiency. The company needed equipment monitoring solutions to bolster the output of its production line processes. The challenge was to find a solution that was compact and flexible enough to be installed in diverse factory environments and support a wide range of machinery and equipment. The company also faced budget constraints due to the realities of global competition, which limited funding for infrastructure investments.
Case Study
How Advantech’s Solutions for Yeefung’s Automated Guided Vehicles Help Turn Traditional Factories into Smart Factories
Yeefung Robotics Technology, a leading provider of comprehensive Automated Guided Vehicles (AGVs) and revolutionary parking solutions in China, was seeking comprehensive hardware and AGV controller solutions. The company wanted to leverage the benefits of Industry 4.0 to ensure that robotics and AGVs work at maximum efficiency with virtually no downtime, leading to reduced costs and increased profits. However, to ensure comprehensive monitoring and flexibility, smart factory AGVs must perform multiple arithmetic operations at speeds that traditional programmable logic controllers (PLCs) simply cannot handle.
Case Study
Upgrading from Manual Transcription to Real-time Monitoring with Advantech’s Industry 4.0 Capabilities
The Ching Luh Group, a leading sports footwear manufacturer, was facing the challenge of automating the collection of real-time production information from manual transcription. The traditional approach of manually recording and entering data into a computer system was cumbersome, slow, and prone to errors and inconsistencies. This outdated method prevented managers from having a firm grasp of the real-time production status, hindering the ability to make meaningful improvements. In today’s fiercely competitive market with rapidly changing customer demands, a shoemaker that persists with this outdated approach risks devastation at the hands of competitors. With the advent of Industry 4.0 and associated smart factory technologies, shoemakers and other textile manufacturers must adapt or die, sink or swim.
Case Study
Advantech Industry 4.0 Solutions, Excellence in Pharmaceutical Manufacturing
União Química, one of the biggest players in Brazil’s burgeoning pharmaceutical industry, was being held back by its reliance on outdated production methods. The firm’s managers found their production lines hampered by a low productivity and a lack of efficient quality monitoring, as well as a lack of remote connectivity enabling easy access to critical production line data. One key distinguishing feature in drug manufacturing is the necessity of carefully documenting each step of the production process for compliance. These strict requirements led pharmaceutical manufacturers to store production information in paper records for future reference, but this approach also made it difficult for production managers to make process improvements.
Case Study
the Early Bird gets the Worm: Advantech’s Edge Gateway Platforms Show How “Industry 4.0” is More Than Just a Catchphrase for an Industrial Laundry Business
The industrial laundry firm, a key player in the textile and service industry, was struggling to transition to Industry 4.0. The firm was traditional and relied heavily on manual labor and old equipment, which lacked open communication interfaces for automation. The management needed to monitor the efficiency of both machines and workers in their large facilities and make use of visualization and data analytics to deploy efficiency initiatives. However, traditional PLC/HMI solutions were too expensive and not easily integrated into cloud-based solutions. Therefore, they needed a dedicated cloud-based application that would allow management to easily view their production efficiency across multiple locations throughout the country.
Case Study
Cutting-Edge Asset Management Solutions for Maximized Efficiency
The Italian manufacturer of transmissions, engines, drivelines, and fasteners sought to develop a company-wide optimization program aimed at enhancing the asset management and energy consumption of their existing machinery and infrastructure. The goal was to improve the condition monitoring process and manage overall equipment effectiveness. The company required an open technology solution for data acquisition and monitoring that could support a range of different equipment and machines without replacing any existing hardware. The system also needed to be user-friendly for operators, with an easy-to-use and intuitive dashboard that could be viewed on a range of devices including smartphones and tablets.
Case Study
With Advantech’s PPC-3120S and EKI Solutions, Production Line Efficiency is Reaching New Heights
The Brazilian manufacturer of consumer goods was facing challenges in maintaining the strictest standards for product quality due to the high volume and complexity of their production facilities. They needed to effectively monitor an extraordinary range of production lines while also maintaining rigorous standards of quality and efficiency. The manufacturer was looking for a solution that could help them actively manage production line assets, make adjustments to coordination, and avoid costly downtime through preventive maintenance. They also needed to ensure the integration of their MES, enterprise resource planning, and maintenance systems for improved machine availability, equipment homologation, and production line management.
同类供应商.
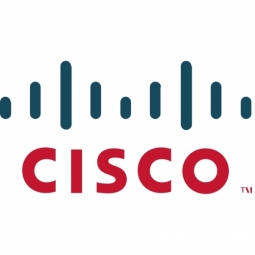
Supplier
Cisco
Cisco designs and sells broad lines of products, provides services, and delivers integrated solutions to develop and connect networks around the world, building the Internet. Over the last 30 plus years, they have been the world’s leader in connecting people, things, and technologies - to each other and to the Internet - realizing their vision of changing the way the world works, lives, plays, and learns.Today, Cisco has over 70,000 employees in over 400 offices worldwide who design, produce, sell, and deliver integrated products, services, and solutions. Over time, they have expanded to new markets that are a natural extension of their core networking business, as the network has become the platform for automating, orchestrating, integrating, and delivering an ever-increasing array of information technology (IT)–based products and services.Subsidiaries/ Business Units: - Jasper - OpenDNS - CloudLock
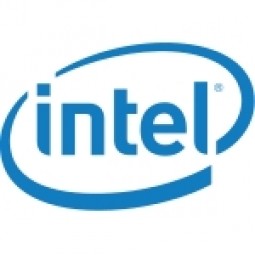
Supplier
Intel
Intel designs, manufactures, and sells integrated digital technology platforms worldwide. The company's platforms are used in various computing applications comprising notebooks, desktops, servers, tablets, smartphones, wireless and wired connectivity products, Wearables, transportation systems, and retail devices. It offers microprocessors that processes system data and controls other devices in the system; chipsets, which send data between the microprocessor and input, display, and storage devices, such as keyboard, mouse, monitor, hard drive or solid-state drive, and optical disc drives; system-on-chip products that integrate its central processing units with other system components onto a single chip; and wired network connectivity products.Featured Subsidiaries/ Business Units:- Intel Inside- Intel Data Center Manager (DCM)- Saffron Technology- Wind River
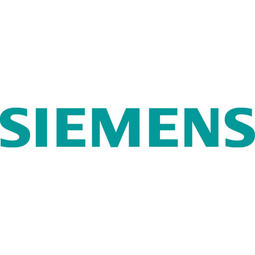
Supplier
Siemens
Siemens is the largest engineering company in Europe. With their positioning along the electrification value chain, Siemens has the knowhow that extends from power generation to power transmission, power distribution and smart grid to the efficient application of electrical energy. Featured Subsidiaries/ Business Units: - Digital Factory - Siemens Technology to Business (TTB)

Supplier
Schneider Electric
Schneider Electric is a leading global manufacturer of equipment for electrical power distribution and for industrial control and automation. The company helps power generators distribute electricity; designs automation systems for the automobile and water treatment industries; builds electric networks and utility management systems for energy, water treatment, oil and gas, and marine applications; and manages electric power in residential, industrial, and commercial buildings.Year founded: 1836Revenue: $26.0 billion (2014)EPA: SUFeatured Subsidiaries/ Business Units:- Avantis- Wonderware